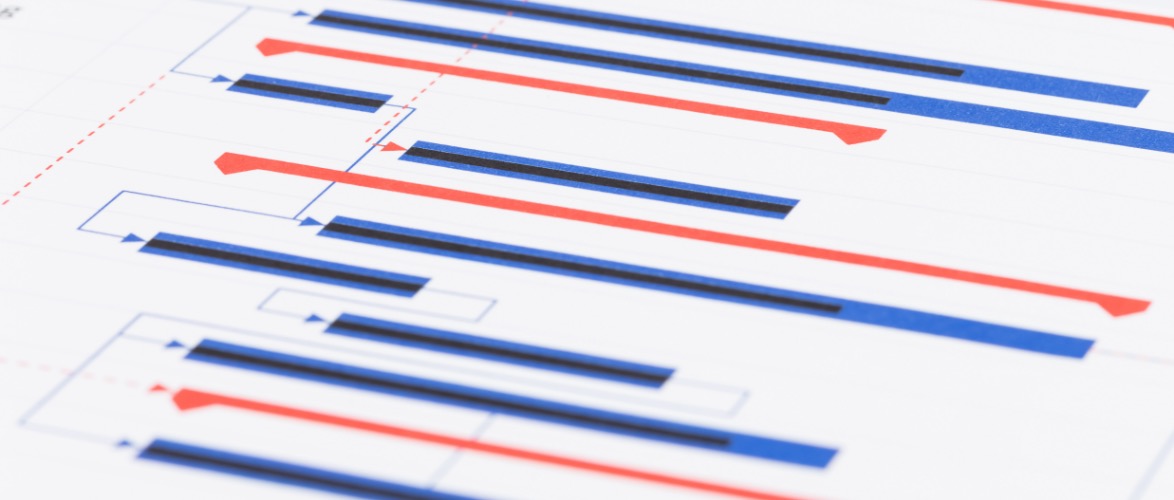
Services
Project Management
At DDG, we recognize the importance of effective overall program management in meeting schedule, cost, and performance goals while mitigating risk.
DDG's Project Management Approach
- Documented and controlled development process
- Complete and thorough specification development
- Detailed schedule development
- Regular status reviews
- Internal design reviews
- Client design reviews and approvals
Development Process
At DDG we follow a disciplined iterative multi-stage gated development process for all projects, with clearly defined requirements, accomplishments and deliverables associated with each stage:
STAGE 1
Marketing Requirements
At this early stage, introductory discussions are conducted with the client to capture the client’s vision for the product and translate that vision into a Marketing Requirements Document (MRD). The MRD covers analysis of the intended market segment, size of opportunity, go-to-market strategy, identification and review of existing competing products, product conceptual design, performance requirements, pricing targets, resulting competitive positioning and advantages in the market, and competitor analysis.
At this stage, DDG Industrial Design (ID) services may be engaged to help the client develop various options in the overall product look and footprint (form, and approximate dimensions).
The MRD helps identify technical problems and facilitates brainstorming of possible engineering solutions and innovations. The scope and extent of the possible technical innovations are discussed as to whether an R&D and proof-of-concept step is necessary. Such discussion serves to identify areas for development of patents and intellectual property (IP). The MRD serves as the guiding document for engineering development. The MRD also establishes the budget for the project, including NRE, which must be agreed to and approved by all parties involved.
STAGE 2
R&D / Proof-of- Concept
At this stage, the underlying technologies are developed and proven. Basic assumptions are tested and confirmed or disproven. Research may be conducted to develop or mature necessary technology that enables the product. Competitor products may be reverse-engineered and analyzed to identify important design considerations, design weaknesses, and areas for improvement and innovation. Hand-built prototype “Proof-of-Concept versions of the product may be developed and produced for testing and evaluation. Such proof-of-concepts may also serve as demonstration units (demos) for investor meetings and solicitation of further investment. Patents and IP may be developed and filed as a result of this stage of development.
At this stage DDG electrical engineering, ID, mechanical engineering and firmware development resources may all be involved in the effort.
A “Go/No-Go” decision is made at this point, depending on whether the outcome was favorable or not. If favorable, the project proceeds.
STAGE 3
Specification Development
One of the keys to successful on-time on-schedule product development is a complete and thorough upfront Product Specification (Product Spec) to drive the detailed engineering tasks. In developing the Product Spec we leverage the MRD, the results of the R&D / Proof of Concept stage and our cross-functional system knowledge to produce a comprehensive document that serves to guide product development through first production. A clear and concise Product Spec, ensures that all product expectations are met or exceeded.
A Product Specification includes:
- Product Overview, including feature Set and the technical approach
- General Requirements, including Design for Manufacturability (DFM), Design for Testability (DFT), Design for Field Accessibility/Serviceability, Design for Reliability.
- Physical Requirements, including Industrial Design (ID), external dimensions, weight, external connections/interfaces, labeling.
- Operational Requirements, including flowcharts and user interface definition.
- Electrical System, including electrical system architecture, sub-assembly and circuit board definition, identification of key circuits and key components.
- Firmware Requirements, including coding standards, source code language, operating systems, update/upgradability, callout of supporting specifications to be developed, listing of Application Program Interfaces (APIs).
- Environmental Requirements, including temperature range, vibration, water intrusion/IP ratings.
- Service Life and Reliability, including the warranty requirements.
- Testing Requirements, including qualification testing, acceptance testing, production testing, and various agency approvals, including UL, CSA, CE, FCC, NSF, RoHS, WEEE, Wi-Fi certification.
- Project Gantt Chart, establishes the overall project execution timeline from start to finish, resource loading, hierarchical task breakdown, reviews, and deliverables.
At this stage DDG Electrical engineering, ID, mechanical engineering firmware development and manufacturing engineering resources may all be involved in the effort. Manufacturing engineering begins the process of engaging possible Contract Manufacturers (CMs), to review and quote the product.
A client’s review and signature approval is required before proceeding.
STAGE 4
Engineering Verification & Testing (EVT)
With an approved Product Spec complete, the development of the actual go-to-market product begins. Detailed electrical engineering, firmware/software development, and mechanical engineering tasks are launched and coordinated via the Gantt Chart, to produce the EVT version of the product. Typically 3-5 samples will be produced, primarily for use by engineering, to serve as the internal development platforms. These samples are produced using low-volume fabrication techniques, such as custom machining, rather than via production tooling. A first version of the formal product design package is produced, including system diagrams, electrical schematics, circuit board designs, mechanical 2D and 3D drawings, and hierarchical costed Bill-of-Materials (BOM). Formal reviews are conducted, including findings, results, and recommendations.
At this stage DDG industrial design, electrical engineering, mechanical engineering firmware development and manufacturing engineering resources may all be involved in the effort. Manufacturing engineering concludes the CM selection process and the CM staff is added to the product team. A formal production test plan is drafted in partnership with the selected CM.
A client’s review and signature approval is required before proceeding.
STAGE 5
Design Verification & Testing (DVT)
The next stage of development is intended to build on the lessons learned from the EVT stage, incorporate design revision, and complete the development of the product. Typically 5 - 10 fully functional samples are produced. These samples are form/fit/function identical to the final production version of the product and are the first units produced off of production tooling. A number of DVT units are allocated for submission to Agencies for review, approval, and certification. DVT units may also be provided to the client for use in limited and informal field verification and validation (Alpha Testing). A second version of the formal product design package is produced, including system diagrams, electrical schematics, circuit board designs, mechanical 2D and 3D drawings, hierarchical costed Bill-of-Materials (BOM), and the production test plan. Formal reviews are conducted, including findings, results, and recommendations.
At this stage DDG electrical engineering, mechanical engineering, firmware development and manufacturing engineering resources may all be involved in the effort. Manufacturing engineering collaborates with the CM on production planning and production documentation, including Standard Operating Procedures (SOPs) and Standard Inspection Procedures (SIPs), Test Plan).
A client’s review and signature approval is required before proceeding.
STAGE 6
Production Verification & Testing (PVT)
The first units to be assembled on the actual production line are the PVT units. The primary purpose of the PVT stage is to verify and validate the production processes at the CM. However, PVT units may also be used by the client to conduct a formal field validation (Beta Testing). Typically 10-50 units are produced. Each manufacturing step is carefully reviewed and evaluated. SOPs and SIPs are redlined and revised for optimal efficiency and throughput. Agency product and factory approvals and certifications are completed. A third and final version of the formal product design package is produced, including system diagrams, electrical schematics, circuit board designs, mechanical 2D and 3D drawings, and a hierarchical costed Bill-of-Materials (BOM). Formal reviews are conducted, including findings, results, and recommendations.
A client’s review and signature approval is required before proceeding. This is the final gate approving production of the product.
STAGE 7
Low-Rate Initial Production (LRIP)
It is important the production is ramped up carefully over the first week or two with an emphasis on quality and close oversight of the production line. Any issues are quickly identified and solutions worked out in collaboration with the CM. Any barriers or limitations to achieving full-rate production are addressed by the cross-functional ramp-up team. LRIP is concluded as production achieves full-rate production with little fallout and acceptable levels of quality.